
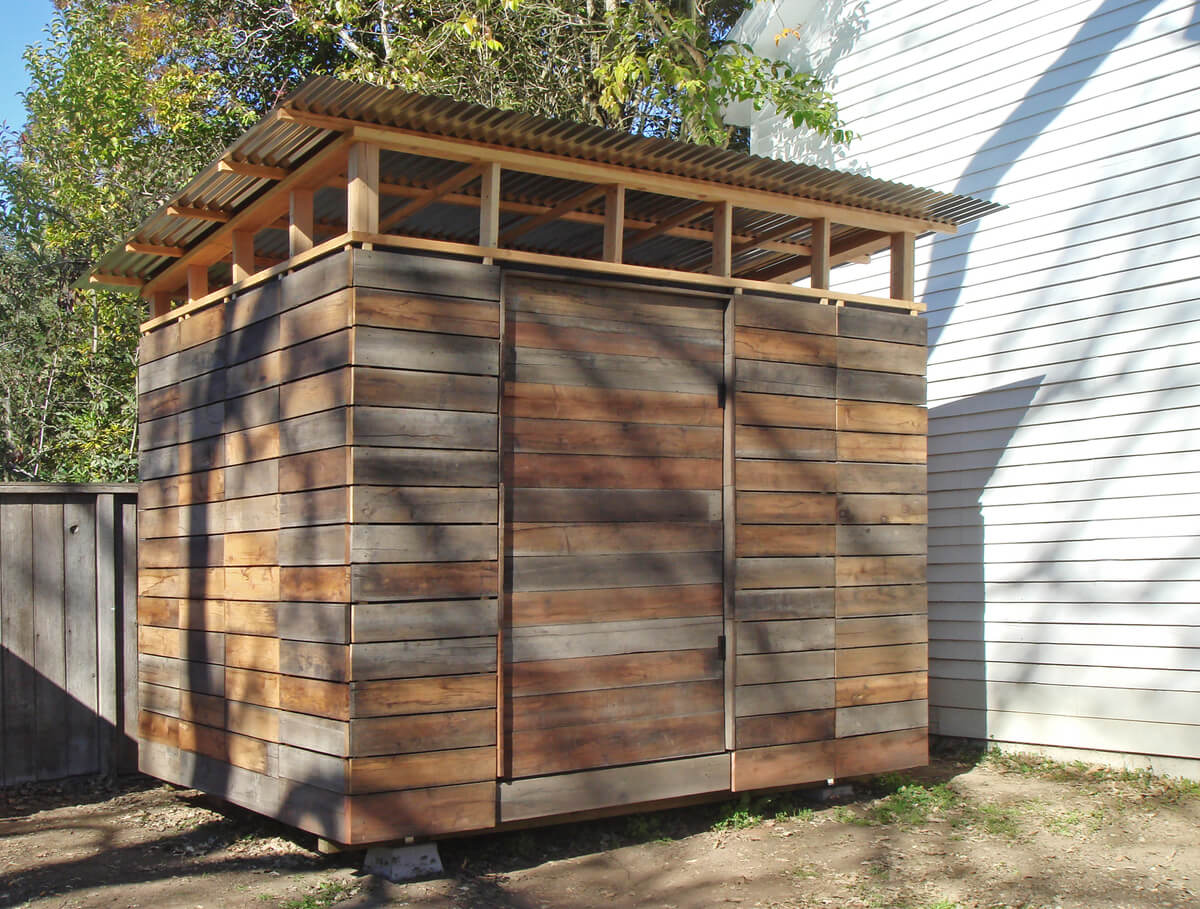

Located overhead out of the way yet at a height I can easily reach to connect a hose to. This is very convenient when I’m using my brad and pin nailers for assembly work. I also installed another connection location above the assembly table / tablesaw. Campbell Hausfeld PA2085 Clean Air System.Campbell Hausfeld PA2121 Standard Air Filters.Campbell Hausfeld H7273 Standard Pressure Regulator.I really like the accessories that Campbell Hausfeld offers including: It’s also important to have a regulator so you can control the air pressure, otherwise you’re at the mercy of whatever pressure is in the tank at any given time. It’s really important to use air filters to remove water and oil (if you’re doing any painting or using tools that can be damaged from oil). I have several terminal locations that I’ve set up including two in the woodworking shop.Īt each location in the shop I have an air filter and a regulator so I can control the air pressure. The relief valve I purchased is slightly higher pressure rated than the tank, but certainly at a pressure much lower than the pipe system which will prevent any possible “disaster” issues.įrom the main branches I soldered 1/2″ copper pipe to each terminal location. While not 100% necessary as the compressor comes with one standard, I wanted an additional level of protection due to the fact that this large compressor is located in the garage where my kids are always coming and going. Each branch is isolated with valves, however the layout is such that each branch can drain back to the start where I have located the drain.īefore I installed the branch lines I installed a secondary pressure relief valve. Every month or so I open the valve and let any water out that’s accumulated in the lines.įrom this point I soldered together3/4″ copper pipe from this location up to the woodworking shop and also a branch for the garage. I created a simple vertical drop of pipe below the first riser with a valve on it. Over time water will condensate inside the lines and you need a way of getting it out.

The next important component is a drain to allow you to drain condensate water from the air lines. You can find these braided hoses used for hydraulic pressure lines. This is pretty important unless you want to fix leaks in the piping due to vibration. The first step in my system is a tank shut off valve right at the tank followed by a flexible braided hose to isolate any vibration from the motor. Another option would be cast-iron but that’s not something I have the skill to do so I went with the copper option. PVC is a brittle material that could cause serious injury if it were to break. I realize some people try to use PVC as it’s cheaper and easier to assemble but I’m not a fan of that idea due to safety concerns. For my system I used copper piping soldered together. For me there were several issues to consider including: Safety, Clean Air and Easy Access. The compressor is the easy part of the system, the harder part in my opinion is delivering the air around the shop. Note: You’ll need to supply your own wiring harness from the motor to a disconnect. Heavy duty CAST IRON oil lubricated twin cylinder pump.The compressor is bolted to the concrete slab to prevent it from moving due to vibration. I installed a Campbell Hausfeld 60 gallon air compressor in the corner of my garage nearest the overhead door and the furthest possible from my house. My woodworking shop is located on the second floor above my garage so I designed a system that would easily serve both locations and the tasks that I do in each. Having a functional, well designed compressed air system is very versatile for any woodworking shop and garage. Workshop Compressed Air Compressed Air System for Workshop and Garage
